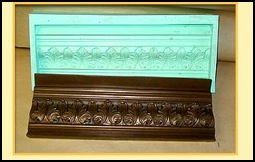
systems (base plus curative; A+B) available in a hardness
range of very soft to medium. Silicones can be cured with either
a platinum catalyst or a tin catalyst. They are available for making
molds that are poured, brushed or sprayed on to a model and
have performance characteristics that no other mold rubber has.
Advantages
–
Silicone rubber has the best release properties
of all the mold rubbers, which is especially an
advantage when doing production casting of resins
(polyurethanes, polyesters and epoxy). No release agent is
required, so there is no post-production cleanup. Silicones
also
exhibit very good chemical resistance and high temperature
resistance (400°F / 205°C and higher). High temperature
resistance
makes silicone the only mold rubber suitable for casting
low
melt metal alloys (i.e. tin, pewter, lead). The combination
of good
release properties, chemical resistance and heat resistance
makes
silicone the best choice for production casting of resins.
Disadvantages
-
Silicones are generally high in cost -
especially platinum-cure. They are also sensitive to
substances
(sulfur clay for example) that may prevent the silicone
from curing (referred to as cure inhibition). Silicones are
usually
very thick (high viscosity), and must be vacuum degassed
prior to pouring to minimize bubble entrapment. If making a
brush-on rubber mold, the time factor between coats is long
(longer than urethanes or polysulfides, shorter than
latex).
Silicone components (A+B) must be mixed accurately by
weight
(scale required) or they will not work. Tin catalyst
silicones will
shrink somewhat and do not have a long library life.
Perma-Flex proudly distributes Smooth-On
Tin and Platinum Silicones
as
well as
Perma-Flex proudly distributes Wacker
Silicones Tin and Platinum Silicones