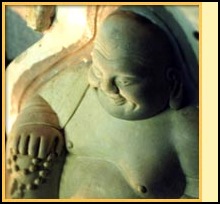
P.U.R.E.-CMC was developed specifically for use with plaster, gypsum and cements. In properly made molds, it releases casts without a parting agent and will not stain or smudge casts taken from it.
It is an exceptionally light compound with a low specific gravity giving it a high yield of rubber per pound. Yet, a given mold often requires less mold material because the strength of the material in a cross-section is quite high. These two features mean less wall and base thickness, less total weight and reduced cost per mold. The two components cure at room temperature and are easily mixed in a one to one ratio by weight through hand stirring or with low speed power mixing. Color coding insures a good blend. Low viscosity produces a very free flowing, penetrating liquid within the fluid time before gel. Good air release and rapid cure permit demolding as specified. The cured rubber has good heat resistance to 100°C., negligible shrinkage in storage and use, and good cold flow resistance. Optimum physical properties are developed in seven days, but the rubber may be used with care during complete cure out of the material.
Lot reproducibility is assured by rigid quality control so each component is interchangeable. Kit parts do not have to be matched.
The P.U.R.E.-CMC Formulations have been designed particularly for use with plaster and Portland cement base materials, providing good release when Perma-Flex P.U.R.E.-CMC MOLD RINSE is used.
P.U.R.E.-CMC PART A is very resistant to water and humidity so there is no gassing due to water pick-up by this component. PART B is a stable, low toxicity isocyanate which has been used successfully in other products for more the 20 years. When exposed to temperatures below 65°F, the material may freeze but simple warming will restore its fluidity and properties.
PREPARATION OF MODELS
Because PERMA-FLEX® P.U.R.E.-CMC Formulations have outstanding flow properties, they will penetrate along and into fine detail to yield excellent reproduction. But care must also be exercised to prevent the mold material from penetrating the surface of the mold itself. The secret to success is proper model preparation. With the use of the specific sealers and/or parting agents on the model, PERMA-FLEX materials will not penetrate the model surface to inhibit formation of the proper surface on the mold and will provide correct release of the model and casts thereafter.
MODELS
Use only a clean model. As required, prepare model by washing, such as with soap and water, until all surfaces are clean, then rinse well with water and allow to fully dry. Seal porous models and porous surfaces. Apply parting compound to all surfaces which the rubber may contact. Recommended parting compounds may be either Perma-Flex POLYURETHANE PARTING COMPOUND or a pure soap parting solution. Polyurethane Rubbers are excellent adhesives, especially P.U.R.E.-CMC Formulations, thus to prevent bonding of the rubber to a model, model pours and surfaces must be filled to prevent a mechanical lock of the rubber to the model and all surfaces well parted so that the rubber will release. Do not use sealing and parting compounds that contain solvents, alcohols or petroleum bases unless all surfaces can be force dried at 100°F for 12 hours to void residual fumes from the work area. Use only such sealers and parting after careful evaluation. To separate P.U.R.E.-CMC Formulations from non-porous surfaces or from themselves, use POLYURETHANE PARTING COMPOUND or Smooth-On Universal Mold Release.
POROUS MODELS
DIRECTIONS FOR POLYURETHANE PARTING COMPOUND
Apply one or more applications of Perma-Flex Polyurethane Parting Compound (PUP), without thinning and buff to a satin gloss. Parting surface must be complete, continuous, and without breaks or dull spots. Brush PUP compound on generously working well into detail. Dry the same brush on a clean rag or paper towel and then pick-up all surplus release material. Let set 8 - 10 minutes or until dry. Then repeat with a second application of release. When dry, brush to a satin gloss with a soft dry brush. Allow PUP compound to dry thoroughly, a minimum of four (4) hours.
NON-POROUS MODELS
Generally, one or more applications of POLYURETHANE PARTING COMPOUND can be used. Customer evaluation is advised prior to molding.
CAUTION
Insufficient sealing and/or parting will allow Perma-Flex molding materials to penetrate and cure within porous surfaces. This will result in a textured and rough surface that interlocks to castings. Such areas will result in adhesion and/or build-up on the mold surface by the casting materials left behind during demolding. Many customers prefer to use their own sealers and partings but such materials should be void of alcohols and water or they will interfere with the cure of the rubber and a tacky surface will result. Many sealers and partings contain solvents which will be absorbed by porous models. Ample time must be allowed to vent all solvent fumes from such materials before molding. Spray sealers and spray partings are not generally recommended as often distribution of the agent is poor and the spray may condense water on the model surface. Customer evaluation of spray sealers and partings is recommended to obtain best success with Perma-Flex products.
SUGGESTIONS
(1) Secure model(s) to pouring surface to prevent floating of model after P.U.R.E.-CMC has been poured over it. A vent hole(s) should be drilled through the pouring table. The model is mounted over the vent hole(s) to allow air to escape to open air rather than into the rubber.
(2) All surfaces where P.U.R.E.-CMC will contact should be prepared with sealer and parting agent as required. Many customers prefer to use their own sealers and partings but such materials should be void of alcohols and water or they will interfere with the cure of the rubber and a tacky surface will result. Many sealers and partings contain solvents which will be absorbed by porous models. Ample time must be allowed to vent all solvent fumes from such materials before molding. Spray sealers and spray partings are not generally recommended as often distribution of the agent is poor and the spray may condense water on the model surface. Customer evaluation of spray sealers and partings is recommended to obtain best success with Perma-Flex products.
(3) Model and surfaces must be dry, thus allow ample time for sealer and parting agents to thoroughly dry before molding.
FORMING OF P.U.R.E.-CMC
Before use, inspect material. If PART A appears cloudy or thick, warm in oven to 100°-110°F until clear. When Part B is exposed to temperatures below 60°F, the material may freeze and often is indicated by crystals within the material, crystals around the inside and lip of the container, being semisolid, and/or a glassy appearance without the presence of crystals. Freezing does not spoil the material, it has just frozen. Warming gently to about 100°F will restore its fluidity and properties. Part B may not be used if frozen, thus on receipt of products and in storage, maintain proper temperatures so that the product is always ready for use. If Part B freezes again due to low temperatures, warm gently until fluid properties return. For consistent time values during application, return all materials to 75°F before use. By maintaining Part B above recommended temperature, and using Part A at recommended temperature, P.U.R.E.-CMC’s will mix easier and be slightly thinner during application, however, you will reduce the work time available to apply the product before it sets. All time values begin when parts are added together.
All parts are somewhat sensitive to moisture or humidity and may pick up a finite amount of water. Perma-Flex polyurethanes are less sensitive than most, but a certain amount of care must be taken. Part A (BASE Polyol) should be kept sealed. Part A may discolor when exposed to air. If Part A is allowed to absorb water, it will show up as gas bubbles or sponginess. To remedy, thoroughly vacuum (less than 5 mm. Hg) before use. Part B (Isocyanate curative) will not only absorb water but will react to it. The first sign will be skinning followed by gelling. When Part B starts to skin, remove skin and use at once or discard. Part B containers should be kept warm, very clean and covered tightly at all times.
Stir well all parts each time before use. To minimize air entrapped within Part B, stir or shake container 24 hours prior to use, then let stand in sealed container to vent air mixed in. If done correctly, ideally Part B should be free of air bubbles when taken from its container.
MIXING
Mixing containers should be non-porous, such as metal, glass or plastic. Paper containers should not be used. The stated ratio for blend is by weight, thus add Part B to Part A in the correct proportion. The ratio for P.U.R.E.-CMC is by weight, 1A to 1B. Mix together until color is homogeneous, about 2-3 minutes depending on quantity and method of mix. STIR COMPLETELY with a stiff flat metal spatula taking care to incorporate materials on bottom and side of container back into mix. Low speed power mixing is suggested on mixes over four pounds using a paddle type mixer. Mix may stand a short time to vent entrapped air introduced during mixing. This step plus pouring the mix over a sharp edge in a thin stream will assist the material’ s natural ability to allow air bubbles to rise away from the model’s surface to yield a quality mold surface. If care during mixing is taken, it will not be necessary to vacuum the mix unless a solid void-free rubber is desired. Pour material in thin stream over sharp edge into prepared assembly allowing pour to flow up and over model. Brushing is not normally necessary. Many times a weak stream of air directed against initial layer will displace any air trapped in detail.
The pour time indicated begins when PART B is added. The mix builds in viscosity until it pours poorly and sets. Temperature of material at time of use and mixing method will vary listed pour and set times.
If additional material is to be added to the initial pouring, additional pours should be completed within 6-8 minutes after initial blend has been made. Although P.U.R.E.-CMC will flow up to 12 minutes, its viscosity greatly increases during its final few minutes of fluid time. Additional pours will disturb the first pour and may result in distortion and imperfections. P.U.R.E.-CMC may be bonded to itself after cure by cleaning the bonding surface with toluol and a soft, absorbent rag. Clean surface once, then with new clean toluol and new rag, clean again for bond. (CAUTION: TOLUOL IS A VERY FLAMMABLE and TOXIC MATERIAL)
Any flexible mold must be on a flat and level surface to avoid distortion transferred through the mold. A backing plate or supporting case is suggested for P.U.R.E-CMC molds. The supporting plate or case is made before mold is first removed from original model by using Ultra-Cal 30 Gypsum Plaster or other low expanding or non-expanding backing materials. After 16 hours, cure is about 90% complete for PL 1040 only. All other P.U.R.E.-CMC’s are about 48 hours. Do not risk distortion by demolding too soon. When removing mold form model, it is recommended that a jet of compressed air be used to start separation. Seven days at room temperature will usually complete full cure and give ultimate physical properties. However, P.U.R.E.-CMC can be used after demolding if no great stress is involved in the use.
PREPARATION OF MOLD FOR CASTING
* For plaster and gypsum cements use Perma-Flex MOLD DRESSING.
* For Portland cement and concrete use Smooth-On In & Out Concrete Release II.
* Wax, not exceeding 200°F, may be poured without parting but to preserve mold use a thin coat of Silicone oil.
* P.U.R.E.-CMC has many of the characteristics of all urethanes and are easy to handle as other kinds of liquids if a few simple precautions are observed.
HANDLING and STORAGE
Part A of the P.U.R.E.-CMC’s series is resistant to water and humidity thus minimizing possible gassing due to water pick up by this component. Part B is a stable, low toxicity isocyanate which has been used successfully with Perma-Flex polyurethanes for many years.
The BASE (Part A-Polyol) should be kept sealed as much as possible. Keeping materials at or above 70°F in a warm, dry place is recommended.
Perma-Flex has available for sale molasses gates for use with P.U.R.E.-CMC when ordered in pail and drum quantities. The use of the gates will aid in preserving the quality of the material.
CLEAN-UP
Excess uncured rubber liquid may be wiped away with paper towels or tissue, followed by paper or cloth moistened with a little solvent such as alcohol, acetone, methyl ethyl ketone or unleaded gasoline to finish. ( EXTREME CAUTION MUST BE USED AS THESE ARE VERY FLAMMABLE LIQUIDS. ) Aromatics like toluol or xylol may be used but are VERY TOXIC.
STORAGE OF CURED MOLDS
Rubber molds may be stored in their supporting cases in any clean, dry and cool location. Heavy objects should never be laid on the molds as some distortion could occur. When rubber is stored on a porous surface or in a porous backing case, such as plaster, apply POLYURETHANE PARTING COMPOUND to all such surfaces in contact with the rubber. If a mold is large and/or with unsupported sections, it is recommended to coat the interior rubber mold surface with POLYURETHANE PARTING COMPOUND and place a splash coat of plaster inside the mold for support.
SAFETY
P.U.R.E.-CMC’s do not contain MOCA or MDI. TDI is not present in any significant amount and all TDI is consumed during cure. As with all such products, the work place should have adequate ventilation. P.U.R.E.-CMC’s are chemical substances and must be handled with respect, therefore protective clothing, gloves and chemical safety goggles are recommended when handling isocyanate compounds. Similar products have been used for years with no reports of discomfort of users. With good personal cleanliness and housekeeping, the worker should not experience any adverse reaction. If an individual is highly allergic, they should not be exposed to Part B Isocyanate. Such people should not attempt to use this product. If the worker has certain allergies, but have not become sensitive to isocyanates, good working practices should allow them to use this product.
CURE and CLEANING
Demold time is largely dependent on temperature and complexity of model. It is recommended that P.U.R.E.-CMC’s cure between 75° and 80°F a minimum of 24 hours before demolding. Cool or cold temperatures will slow cure, thus delaying demolding. Do allow ample time where possible for cure to avoid tearing of the rubber during demolding and work rubber from model carefully. If available, demold with the aid of compressed air. To clean a mold, make one or two waste cast with plaster to remove contaminations from the mold surface. Also, the rubber may be washed in PURE-CMC MOLD RINSE or a 30% pure natural soap. Do not use alcohols, solvents and/or petroleum base liquids, or products containing such materials, to clean or cast into any polyurethane rubber as shrinkage will result.
Often a waste mold is made to duplicate a surface, then a plaster cast is made into the waste mold to obtain a model for further refinement of detail and/or dimensions. Of course, if the original model has sufficient quality that is duplicated by the rubber, the waste mold can become a production mold. If however, the duplication requires refinement, a second production mold will be required. P.U.R.E.-CMC’s may be used.
CASTING
Plasters may be cast directly into P.U.R.E.-CMC’s without a release agent. However, the use of either Perma-Flex MOLD DRESSING or PURE-CMC MOLD RINSE to eliminate pin holes, a common problem when casting plaster, is suggested. To cast cements, P.U.R.E.-CMC’s should be prepared with Perma-Flex MOLD RINSE as directed. As a general rule, we do not recommend polyurethanes to cast waxes and resins, but customers have had limited success when prototype casting of such products. Wax castings made in P.U.R.E.-CMC’s may not require a parting agent, but a parting agent will be helpful to reduce stickiness and is required for hot waxes. To cast a resin, a barrier must be established that is complete, continuous and without breaks. A suggested parting agent for this application world be U-10 MOLD RELEASE. Testing for compatibly and release is highly recommended.
P.U.R.E.-CMC is available in two formulations as described in this product data sheet. In most molding requirements, the proper methods of use between formulations are similar. However, since there are differences, all properties will not be the same. For example, Shore A Durometer, viscosity, tensile, tear, elongation, pour and cure times will vary from that described in the P.U.R.E.-CMC data sheet.
Formulation BP-50 is a brush applied polyurethane rubber provided in a semi-paste form to make laminated and glove molds. BP-50 is ideally suited for vertical and overhead surfaces where a material is required to stay in place during mold development, such as on site restoration work where a mold must be pulled from an existing structure and then used to cast a duplication of the original design. The BP (brushable polyurethane) system is a specially modified system of our well established line of PURE-CMC polyurethane elastomers and have been developed to meet the most stringent requirements for handling, curing and use. The BP Formulation have a specific data sheet and is available upon request.
CAUTION
These products contain plasticizers. Liquid or cured rubber in direct contact with lacquered or painted surfaces may be damaged and further inhibit the cure of the rubber.
Inasmuch as the Perma-Flex Mold Company has no control over the exact manner in which others may put these materials to use, we do not guarantee that the same results as those described herein will be obtained.
WARRANTY
Products manufactured by The Perma-Flex Mold Company are produced to meet our manufacturing and sales specifications. We warrant that goods shipped by us meet these specifications; but because their use is beyond our control, we accept no responsibility or liability for damages or any injury resulting from the use or handling of these materials. In cases where our products are found not to conform to our specifications, our liability is limited to the purchase price of the goods proved to be defective. The Perma-Flex Mold Company makes no warranty that these products are merchantable or fit for any particular purpose, nor is there any other warranty, expressed or implied, except as is expressly provided herein.
Formulation Shore A Component Mixing Ratio Pour Time Demold Time Cure Time Color
Number Durometer Parts (by weight) (minutes @ 80°F) (hours @ 80°F) (days @ 80°F)
PL-1040 37-39 A:B 1:1 10 24 3 Green
PL-4042 35 A:B 1:1 10 24 3 Brown**
** No coloring agent needed. The natural color of P.U.R.E.-CMC will be a brown hue. As the product ages, either in storage or cured form, the product will become darker.
INTRODUCTION
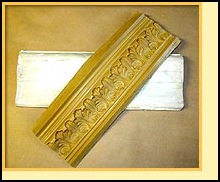
Formulation BP-50 is a brush applied polyurethane rubber provided in a semi-paste form to make laminated and glove molds. BP-50 are ideally suited for vertical and overhead surfaces where a material is required to stay in place during mold development, such as on site restoration work where a mold must be pulled from an existing structure and then used to cast a duplication of the original design. The BP (brushable polyurethane) system is a modification to our well established line of PURE-CMC polyurethane elastomers and has been developed to meet the most stringent requirements for handling, curing and use.
Following cure, P.U.R.E.-CMC Formulation BP-50 forms a high modulus polyurethane rubber. Formulation BP-50 is a stiff, higher viscosity Shore A Durometer 45 elastomer offering great strength. Molds made with BP-50 offer excellent flexibility with accurate dimensions. Quality of each lot is assured so that unit parts do not have to be matched.
Part A of BP formulation is provided in a semi-paste form to permit lamination of a polyurethane elastomer by brush or trowel when blended correctly with Part B, the catalyst. Curing proceeds readily at recommended temperatures, 75° to 80°F. The cured elastomers show heat resistance to 200°F, negligible shrinkage in use or storage when used as recommended.
Formulation BP-50 haas been designed particularly for use with plaster and Portland cement base materials, providing good release when Smooth-On In & Out II, concrete release agent is used.
APPLICATION
BP-50 may be used directly as the rubber mold compound to develop a mold, do not dab on, but work from the bottom to the top of the model when applying this product. Sufficient work time is available to utilize proper brush coat techniques when apply BP-50 to void the contact surface of air. BP-50 has the characteristics of a buttery type paste. As required, apply additional coats until the model is totally covered with rubber. The minimum cross section thickness of BP-50 should be between 1/8 to 1/4 inch. As the rubbers is cured by a catalyst, cure is possible in a thin and thick section, thus allowing back drafts and undercuts to be filled during mold development making for quick buildup and completion of the mold, During cure, BP-50 do not involve any evaporation as will water carried rubbers like Latex, therefore, shrinkage, curling and ample drying time between layers of the rubber are not problems.
THINNING
Formulation BP-50 may be thinned 3% by weight using Mineral Spirits #135 or kerosene added to the BP-50 mix to reduce viscosity for the initial coat of rubber only over detail, thus reducing the chance of entrapped air on the first coat. When Mineral Spirits #135 or kerosene is used to thin, use only on the initial layer to form a thin skin and do not thin additional layers with Mineral Spirits #135 or kerosene.
MODELS
Use only a clean model. As required, prepare model by washing, such as with soap and water, until all surfaces are clean, then rinse well with water and allow to fully dry. Seal porous models and porous surfaces. Apply parting compound to all surfaces which the rubber may contact. Recommended parting compounds may be either Perma-Flex POLYURETHANE PARTING COMPOUND, a pure soap parting solution or Smooth-On's Universal Mold Release. Polyurethane Rubbers are excellent adhesives, especially BP-50, thus to prevent bonding of the rubber to a model, model pours and surfaces must be filled to prevent a mechanical lock of the rubber to the model and all surfaces well parted so that the rubber will release. Do not use sealing and parting compounds that contain solvents, alcohols or petroleum bases unless all surfaces can be force dried at 100°F for 12 hours to void residual fumes from the work area. Use only such sealers and parting after careful evaluation. To separate BP’s from non-porous surfaces or from themselves, use POLYURETHANE PARTING COMPOUND.
PREPARATION
Prior to mixing, determine the amount of rubber to be mixed and applied within the work time available. BP-50 has a work time of 20 minutes at 75°F. If the material temperature is allowed to fluctuate, so will time values available, handling properties and final cure out of the rubber.
MIXING
The stated ratio for blend is by weight, thus add Part B to Part A in the correct proportion. The ratio for BP-50 is by weight, 2A to 1B. Blend may be made in any clean, non-porous container, on glass or a hawk. A stiff, broad tool or trowel should be used to mix until a homogenous blend is made. Attention to weight proportions and mixing procedures is required for complete and proper cure. A good method to mix is to place Part A on a flat surface forming a lake from it, then place Part B inside the lake. Mix Part A into Part B as if it were cement.
HINTS
(1) If product is applied by brush, following blend of Part A and B, place a small quantity into a non-porous container. Insert brush(s) to be used into this container and work brush in the rubber to remove air from bristles. Discard this rubber and do not use as it will be loaded with air. A disposable, stiff bristle brush is recommended.
(2) If a trowel is used, soap the trowel to minimize rubber sticking to the trowel during application. Wipe excess soap parting off before use.
(3) To obtain a smooth surface on the final layer, put on a pair of rubber gloves and soap up gloves and hands with a 30% pure soap solution. Wipe excess soap off before working with rubber. About 5 minutes after the rubber has set, lightly work the exterior of the final layer to a smooth surface and remove tool marks.
(4) If original containers are to be reused at a later time to withdraw more material, apply a light application of a silicone oil to the threads and lip of each container before use to allow for easier opening later.
REINFORCEMENT AND BACKING
Laminated molds, if desired, may be internally reinforced in areas of stress or throughout. Open weave, clean natural fiber cloth is best for reinforcement. If used, the cloth is placed in a layer of lamination by thoroughly saturating the cloth in the catalyzed rubber, then laying the cloth onto the surface and working out entrapped air. The initial layer of rubber covering the model should be cured to prevent the cloth from breaching the mold surface. Follow up with an additional layer(s) of rubber until the fabric is totally buried. For support and alignment of the rubber mold, prior to demolding the rubber from the model, a glove or laminated mold must be backed with a rigid supporting case(s) which can be made by using U.S.G. ULTRA-CAL 30 or U.S.G. ULTRA-CAL 60 plaster, BP-50, or fiberglass. To allow plaster cases to separate easier from the mold, one application of Perma-Flex POLYURETHANE PARTING COMPOUND applied to the cured rubber is helpful. To separate BP-50 or fiberglass from the cured rubber, use U-10 URETHANE MOLD RELEASE. Customers have found, that in selected applications, laminated molds backed with BP-50 will provide suitable hardness to the mold and eliminate the need for a rigid supporting case when BP-50 is applied to sufficient thickness. In all cases, a rubber mold must have proper support to maintain registration.
CURE and CLEANING
Demold time is largely dependent on temperature and complexity of model. It is recommended that BP’s cure between 75° and 80°F a minimum of 24 hours before demolding. Cool or cold temperatures will slow cure, thus delaying demolding. Do allow ample time where possible for cure to avoid tearing of the rubber during demolding and work rubber from model carefully. If available, demold with the aid of compressed air. To clean a mold, make one or two waste cast with plaster to remove contaminations from the mold surface. Also, the rubber may be washed in PURE-CMC MOLD RINSE or a 30% pure natural soap. Do not use alcohols, solvents and/or petroleum base liquids, or products containing such materials, to clean or cast into any polyurethane rubber as shrinkage will result.
Often a waste mold is made to duplicate a surface, then a plaster cast is made into the waste mold to obtain a model for further refinement of detail and/or dimensions. Of course, if the original model has sufficient quality that is duplicated by the rubber, the waste mold can become a production mold. If however, the duplication requires refinement, a second production mold will be required and either BP’s or a poured in place rubber such as PURE-CMC may be used.
CASTING
Plasters may be cast directly into BP-50 without a release agent. However, the use of either Perma-Flex MOLD DRESSING to eliminate pin holes, a common problem when casting plaster, is suggested. To cast cements, BP-50 should be prepared with Smooth-On's In & Out II, concrete release agent, as directed. As a general rule, we do not recommend polyurethanes to cast waxes and resins, but customers have had limited success when prototype casting of such products. Wax castings made in BP-50 may not require a parting agent, but a parting agent will be helpful to reduce stickiness and is required for hot waxes. To cast a resin, a barrier must be established that is complete, continuous and without breaks. A suggested parting agent for this application world be Smooth-On's Universal Mold Release. Testing for compatibly and release is highly recommended.
HANDLING and STORAGE
Part A of the BP-50 series is resistant to water and humidity thus minimizing possible gassing due to water pick up by this component. Part B is a stable, low toxicity isocyanate which has been used successfully with Perma-Flex polyurethanes for many years. When Part B is exposed to temperatures below 60°F, the material may freeze and often is indicated by crystals within the material , crystals around the inside and lip of the container, being semisolid, and/or a glassy appearance without the presence of crystals. Freezing does not spoil the material, it has just frozen. Warming gently to about 100°F will restore its fluidity and properties. Part B may not be used if frozen, thus on receipt of products and in storage, maintain proper temperatures so that the product is always ready for use. If Part B freezes again due to low temperatures, warm gently until fluid properties return. For consistent time values during application, return all materials to 75°F before use. By maintaining Part B above recommended temperature, and using Part A at recommended temperature, BP’s will mix easier and be slightly thinner during application, however, you will reduce the work time available to apply the product before it sets. All time values begin when parts are added together.
All parts are somewhat sensitive to moisture or humidity and may pick up a finite amount of water. Perma-Flex polyurethanes are less sensitive than most, but a certain amount of care must be taken. Part A (BASE Polyol) should be kept sealed. Part A may discolor when exposed to air. If Part A is allowed to absorb water, it will show up as gas bubbles or sponginess. To remedy, thoroughly vacuum (less than 5 mm. Hg) before use. Part B (Isocyanate curative) will not only absorb water but will react to it. The first sign will be skinning followed by gelling. When Part B starts to skin, remove skin and use at once or discard. Part B containers should be kept warm, very clean and covered tightly at all times.
Stir well all parts each time before use. To minimize air entrapped within Part B, stir or shake container 24 hours prior to use, then let stand in sealed container to vent air mixed in. If done correctly, ideally Part B should be free of air bubbles when taken from its container.
SAFETY
BP’s do not contain MOCA or MDI. TDI is not present in any significant amount and all TDI is consumed during cure. As with all such products, the work place should have adequate ventilation. BP’s are chemical substances and must be handled with respect, therefore protective clothing, gloves and chemical safety goggles are recommended when handling isocyanate compounds. Similar products have been used for years with no reports of discomfort of users. With good personal cleanliness and housekeeping, the worker should not experience any adverse reaction. If an individual is highly allergic, they should not be exposed to Part B Isocyanate. Such people should not attempt to use this product. If the worker has certain allergies, but have not become sensitive to isocyanates, good working practices should allow them to use this product.
CAUTION
These products contain plasticizers. Liquid or cured rubber in direct contact with lacquered or painted surfaces may be damaged and further inhibit the cure of the rubber.
CLEAN-UP
Excess uncured rubber liquid may be wiped away with paper towels or tissue, followed by a paper or cloth moistened with a little solvent such as alcohol, acetone, methyl ethyl ketone or unleaded gasoline to finish. ( GREAT CAUTION SHOULD BE USED AS THESE ARE VERY FLAMMABLE LIQUIDS ! ) Aromatics like toluol or xylol may be used but are very toxic.
STORAGE OF CURED MOLDS
Rubber molds may be stored in their supporting cases in any clean, dry and cool location. Heavy objects should never be laid on the molds as some distortion could occur. When rubber is stored on a porous surface or in a porous backing case, such as plaster, apply POLYURETHANE PARTING COMPOUND to all such surfaces in contact with the rubber. If a mold is large and/or with unsupported sections, it is recommended to coat the interior rubber mold surface with POLYURETHANE PARTING COMPOUND and place a splash coat of plaster inside the mold for support.
Inasmuch as the Perma-Flex Mold Company has no control over the exact manner in which others may put these materials to use, we do not guarantee that the same results as those described herein will be obtained.
WARRANTY
Products manufactured by The Perma-Flex Mold Company are produced to meet our manufacturing and sales specifications. We warrant that goods shipped by us meet these specifications; but because their use is beyond our control, we accept no responsibility or liability for damages or any injury resulting f rom the use or handling of these materials. In cases where our products are found not to conform to our specifications, our liability is limited to the purchase price of the goods proved to be defective. The Perma-Flex Mold Company makes no warranty that these products are merchantable or fit for any particular purpose, nor is there any other warranty, expressed or implied, except as is expressly provided herein.