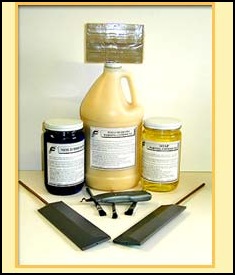
Polyurethane Parting Compound (PUP)
Because PERMA-FLEX® materials have outstanding flow properties, they will penetrate along and into fine detail to yield excellent reproduction. But care must also be exercised to prevent the mold material from penetrating the surface of the mold itself.
The secret to success is proper model preparation. With the use of the specific sealers and/or parting agents on the model, PERMA-FLEX materials will not penetrate the model surface to inhibit formation of the proper surface on the mold and will provide correct release of the model and casts thereafter.
POROUS MODELS
All models should be thoroughly dry. Seal surface to prevent penetration with PERMA-FLEX POLYURETHANE PARTING COMPOUND. Apply one or more applications of Perma-Flex Polyurethane Parting Compound (PUP), without thinning and buff to a satin gloss. Parting surface must be complete, continuous, and without breaks or dull spots. Brush PUP compound on generously working well into detail. Dry the same brush on a clean rag or paper towel and then pick-up all surplus release material. Let set 8 - 10 minutes or until dry. Then repeat with a second application of release. When dry, brush to a satin gloss with a soft dry brush. Allow PUP compound to dry thoroughly, a minimum of four (4) hours.
NON-POROUS MODELS
Generally, one or more applications of PUP can be used. Customer evaluation is advised prior to molding.
CAUTION:
Insufficient sealing and/or parting will allow Perma-Flex molding materials to penetrate and cure within porous surfaces.
This will result in a textured and rough surface that interlocks to castings. Such areas will result in adhesion and/or build-up on the mold surface by the casting materials left behind during demolding. Many customers prefer to use their own sealers and partings but such materials should be void of alcohols and water or they will interfere with the cure of the rubber and a tacky surface will result. Many sealers and partings contain solvents which will be absorbed by porous models. Ample time must be allowed to vent all solvent fumes from such materials before molding. Spray sealers and spray partings are not generally recommended as often distribution of the agent is poor and the spray may condense water on the model surface. Customer evaluation of spray sealers and partings is recommended to obtain best success with Perma-Flex products.
MOLD DRESSING
MOLD DRESSING is used to “wet” a mold surface by reducing surface tension on most finished flexible molds such as our polysulfides, urethanes, latex, silicones and vinyls, wherein plaster or gypsum cements are cast to obtain pinhole free reproductions.
DIRECTIONS (for Mold Dressing) Dilute at the rate of one-half pint PERMA-FLEX MOLD DRESSING in three gallons of water. Wash mold thoroughly in clean water, then rinse mold in the MOLD DRESSING solution. Drain mold before casting. Do not allow MOLD DRESSING to dry on mold surface. Pour plaster while mold is still “wet” with MOLD DRESSING.
Other Suggestions:
Mix fresh each day. Old solution may be used for prewashing molds. For cleaning new or soiled molds, work up lather over face of mold with a small amount of undiluted PERMA-FLEX MOLD DRESSING and rinse thoroughly with clean water before using.
SOAP PARTING COMPOUND
Apply generously with brush or sponge. Work into rich lather, allow to set 3 - 5 minutes, then remove surplus soap lather, giving special attention to fine detail and undercuts. Repeat this operation 5 - 7 times until model is thoroughly sealed. Soap Parting should dry 10 - 15 minutes, then buff to satin shine with soft brush or cloth. Use water to thin if necessary.
“The secret to success is proper model preparation.”